The fact of the engine being a Chevrolet LS3 was set in stone as the chassis has the correct mounts for that engine. It does come in a variety of power outputs. The basic crate engine is quoted as 430bhp, then with different camshafts we get up to 525bhp. There are murmurs about whether a 525bhp version will pass IVA emissions test. Some folk say just dial down the mixture for the test, others says it's not that simple. With a specialist build the LS3 can be up over 575bhp. But it all comes at a cost.
Regardless of the state of tune, the main thing is how to source the engine.
I costed up obtaining parts and building it myself. it worked out more expensive than a crate engine off the shelf.
I discussed with various folk about appointing a specialist builder. One company said that unless I need a special build for racing, don't bother as the cost is not worth it. There are individuals who will build engines. I have had various good and bad reports. For the kind of money we are talking about I want to have a reasonable assurance that the supplier is going to be around in the event of problems.
Next was to look at sourcing a crate engine from a supplier in the States. Their quotes are about the same as in the UK with VAT. Add in transport and import stuff and that makes no sense. Which is a shame as these things are everywhere in the States, you'd think they would be cheap as chips. I did make contact with an engine builder in California who promised a bespoke build to my own spec way cheaper than I can get in the UK. Sadly no quote was actually forthcoming despite a couple of attempts at chasing it.
The thing is that a standard crate engine won't fit in a AK Gen III chassis. It needs a bit of work. The oil pan has to be changed to a 'F' body type. There are changes to the alternator mounting bracket and power steering pump. And the exhaust headers will be the wrong type. The correct headers are not easily available it seems.
So what to do.
The answer is phone up Brain at Roadcraft, put an order in for a LS3 430bhp and a Tremec TKO600 'box. Roadcraft know all about AK Cobra chassis and will supply everything you need for the engine to drop straight in with no worries.
There are cheaper ways of getting a power plant if you put the effort in to get an old engine and refurb it etc. But this is by far the easiest and the least hassle.
Regarding the Tremec 'box. It comes with two different 5th gear ratios. .82 and .64. The .82 is a closer ratio and you will be pulling about 700rpm more than with .64 5th gear. The .64 option is quite a big drop in revs when changing up from 4th. It is probably a proper overdrive and gets you a bit better fuel consumption and a more relaxed ride on the motorways. The potential issue is that around 60 - 65 when you want to change up, the revs may drop out of the usable torque curve and the engine gets bogged down. Especially true if engine is in a higher state of tune where the usable torque is pushed further up the rev range. I went for the .82 as I think it will be more usable under most circumstances.
What I did want though is to get the engine from Roadcraft as a crate engine and do all the work myself assembling the Serpentine belt and pulley systems at the front, swapping over the oil pan and assembling the clutch and flywheel.
It saves a few bob and is nice to get intimately acquainted with your weapon of choice for power. Roadcraft will supply everything you need boxed and ready for assembly.
Delivery:


I am very pleased to say that I happen to know a splendid chap called James who loaned me his engine hoist. Here the engine is resting on part of the original crate it arrived in while I work on it. Saved money on buying/hiring an engine stand.
Changing the oil pan means laying underneath the block. So I secured the arm of the hoist to a rafter in case the hydraulic unit failed. This also doubles up to relieve pressure on the hydraulic unit.
Before you start, remove this thing:
It is at the front near side of the engine and has a black plastic pipe connecting to a port in the air intake body.
It is a sensor called EVAP. The ECU harness will not be using it and you will need the port, that the end of the plastic tube connects to, for the idle motor when you get it from AK.
Unless you are using fly-by-wire throttle that is in which case you don't need an idle motor.
Next, change the oil pan. It is a no brainer except that when fitting the new pan, do not tighten the bolts until the bell housing has been temporarily bolted on the back. The lower part of the oil pan butts up against the bell housing and it must be aligned so the oil pan doesn't put the bell housing out of line. Also use some grey RTV gasket at the corners. The original residue shows where.
Then assemble brackets, alternator, power steering pump, pulley, tensioner and power steering pump reservoir.
The pump and pulley mount on the alternator bracket. There is smaller bracket that provides rigidity to the pump. There are three bolts securing it through the pump wheel here:

There is a small black bracket for the pump reservoir that fits to two of the alternator bracket bolts. I removed the label after the photo!

There is a small tube that connects the pump reservoir to the pump.
The outlet to the steering rack is at the bottom of the pump. Keep it blocked off until ready to install the line.
And here it is. The tensioner is on the far left. Use a socket and bar on the central nut to move the tensioner in to get enough slack to slip the belt on.

Torque settings are:
10mm bolts: 38lb/ft
8mm bolts: 18 lb/ft
8mm oil pan bolts: 18 lb/ft
6mm long oil pan bolts: 9 lb/ft.
At the rear we find the clutch and bell housing.
Remove the flywheel if it is fitted.
Clean all bell housing and crankshaft surfaces.
Install the bell housing with all retaining bolts tightened to spec.
Install the magnetic mount for the dial gauge through the housing and mount securely on the end of the crankshaft. It doesn't have to be central, it can be offset from the crank centre line, but it MUST be flush with the crank surface.
Set the dial gauge so it is going to read on the inner surface of the opening to the bell housing.

Remove the spark plugs so we can turn the engine over more easily.
At the front, looking at the front, the crankshaft rotation is clockwise when running. That is to say a socket on the central pulley will be in the 'tightening' up direction. I put a crack bar on it so I can move the crank round.
Set the dial gauge to zero at 12 o'clock. Turn the crank to take readings at 9, 6 and 3 o'clock. Return to 12 o'clock and check the gauge is back at zero to check it has not moved.

The maximum offset is 5 thou.
My readings were:
12 o'clock = 0.00mm
9 o'clock = +0.03mm (1 thou)
6 o'clock = +0.01mm (0.4 thou)
3 o'clock = -0.05mm (2 thou)
This was checked 5 times with the dial gauge reseated twice.
It seems the block and housing are quite well engineered.
If you have more than 5 thou variance you may need offset dowel pins, or you have a dodgy crank or block or dial gauge, or all three.
Installing the flywheel.

The threaded holes for the flywheel bolts are drilled all the way through to the engine internal.
So there is a risk of oil under pressure seeping past the bolts into the clutch area. Use a reasonable amount of blue loctite or else grey RTV gasket stuff.
Have a small amount of grease under the bolt heads so as to relieve friction when torquing them up.
The bolts are tightened in at least three passes. And torque them in crossed order.
1st pass 15 lb/ft
2nd pass 37 lb/ft
3rd pass 74 lb/ft
Install the crank centre bearing with the lip/flange to the outside. It is an interference fit and needs to be drifted in with a 34mm socket or similar. Make sure it is correctly seated.
Next comes the clutch friction plate held in place by a 36 spline, 1 1/8 dia clutch plate tool.
Finally install the clutch pressure plate. Heavy bugger it is too.
Take many passes to tighten the bolts (blue loctite) as we are now compressing the clutch release springs.
1st pass = 11 lb/ft
2nd pass = 26 lb/ft
3rd pass = 41 lb/ft
final pass = 52 lb/ft


Take note about how the release bearing sits in the fork. The spring tabs must be inside the outer flange of the bearing.
If you have the starter motor, now is a good time to attach it and check the clearance between the starter gear and the ring gear on the flywheel. There should be .040 - .100 thou gap. Check this before installing the bell housing.
On with the bell housing.
Housing bolts = 37 lb/ft torque
Grease the far end of the gearbox shaft that goes into the spigot bearing in the crankshaft.
Line the box up and gently rock it to match the splines with the clutch plate. Operate the clutch release arm to make sure the bearing is free and not jamming on the shaft.
When the hub of the gearbox is about to go into the housing, the shaft will be engaged in the spigot bearing. Install the four bolts and gently pull the box into the housing. Make sure to keep the box exactly square to the housing as it goes in.
I cannot finally tighten these bolts up as the two on the left are also used to mount the clutch slave cylinder bracket which I don't yet have.
Put a block under the rear of the box to take the weight off its feet.
Final thing is to remove the exhaust headers and see if we can flog them on ebay.
I don't have the correct headers yet but AK assure me they will go on after the engine is installed in the chassis.
Installation in Chassis
Two essential items: A hoist, and a chap called Dale:
You'll need the hoist with an attachment that can alter the angle of the engine as it slides in.
And you'll need Dale to help sight the engine going in, to provide some wisdom about fitting engines and to help with tea drinking and cake eating. You can probably make do with a chap who is not called Dale, but I can't guarantee the same results. Anyway, thanks Dale
I jacked the rear of the car as high as I could get it. Mainly so I can get underneath to drill and fix the bolts that secure the gearbox bracket. But it also helps with the angle the engine needs to be relative to the chassis.
Cover nearby chassis tubes to protect against knocks from the engine. I used some water pipe insulators. Remove exhaust headers if they are fitted. The starter motor and clutch slave can go on later.

At one point we had to remove the chains that were connected to the rear of the cylinder head and replace with rope down to the gearbox and a jack under the gearbox. Leaving them in place means there would have been no room to remove the bolts that secured the chain brackets as they line up with one of the chassis tubes.
The chassis rails which the gearbox mount bolts to is 3.2mm thick. I used four 10mm bolts straight into the chassis, I don't think rivnuts would provide very much more, and will need 13mm holes drilled. You can drill right through and weld studs from the top (make sure it is finished flush as I think the body needs to sit here). But wisdom from AK suggests the four 10mm bolts are sufficient.
Propshaft
Before fitting this, you may want to check the section on fitting the speedo sensor:
18 Speedo Sensor
From Bailey Morris as per everyone else.
There is a long spigot protruding from the diff flange which the propshaft flange has to slide over.
In order to get the maximum length of slip yoke onto the splines in the gearbox shaft I cut the spigot length down. The issue is that whatever length the spigot is, that is the amount which the slip yoke is not engaged in the gearbox. I'm not sure of the length of the splines in the 'box but I only have a couple of centimetres protruding so there is lots of engagement.

The slip yoke is from Roadcraft. I had to send it to Baileys so they can use it to assemble the shaft.
Baileys also supply these so next time check their prices, saves a bit of faffing with parcels back and forth.
If you have a TKO600 'box, you may have a large donut of rubber sticking out the back.
This has to be removed. Details on various websites make mention of a smaller rubber ring that can be left in place and pushed into the 'box when inserting the slip yoke.
I had this:

And it was a right bugger to get out. Use two pliers, grip hard and pull like mad.
Don't insert anything up it to try to free it. The gearbox seal is behind it and you don't dare damage that. It is really hard to pull out, but out it must come.
The retaining bolts may not easily insert into the shaft flange. I used hex bolts but still needed to shave some metal. There are three points of interference, the entry and exit of the flange holes and a corner of the UJ joint on the shaft. Grind a tiny amount from each location until the bolt slips through. The bolts need to be inserted before the shaft is fitted so the angle of the UJ joint can be used to best effect for inserting the bolts.
The measurements for Bailey Morris are the number of holes in the diff flange (three or four) and the distance from this flange to where you want the slip yoke to be in the gearbox.
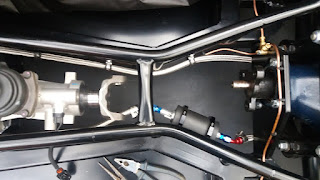
So in this case it is the distance from the face of the diff flange to the center line of the UJ joint holes in the slip yoke.
When all done there is no room to get a torque wrench on them so lean on a spanner until your face goes Ferrari Red.

This pic also shows the relative position of the fuel pump to the shaft which is fine with good clearance.